Caterpillar 3408 Injection Pump Service Manual
Download Ebook Caterpillar 3408 Injection Pump Service Manual Caterpillar 3408 Injection Pump Service Manual As recognized, adventure as skillfully as experience about lesson, amusement, as skillfully as contract can be gotten by just checking out a books caterpillar 3408 injection pump service manual as well as it is not directly done, you. About Press Copyright Contact us Creators Advertise Developers Terms Privacy Policy & Safety How YouTube works Test new features Press Copyright Contact us Creators. Caterpillar 3208 FUEL INJECTION PUMP HOUSING AND GOVERNOR DISASSEMBLY & ASSEMBLY.Remove Fuel Injection Pump Housing & Governor TOOLS NEEDED A B. Caterpillar 3406 3408. I do remember there was an incorrect pin assignment in the service manual wiring.
INSTANT DOWNLOAD
Complete workshop & service manual with electrical wiring diagrams for Caterpillar 3408C, 3412C, 3412D Engines. It’s the same service manual used by dealers that guaranteed to be fully functional and intact without any missing page.
This Caterpillar 3408C, 3412C, 3412D Engines service & repair manual (including maintenance, overhaul, disassembling & assembling, adjustment, tune-up, operation, inspecting, diagnostic & troubleshooting…) is divided into different sections. Each section covers a specific component or system with detailed illustrations. A table of contents is placed at the beginning of each section. Pages are easily found by category, and each page is expandable for great detail. The printer-ready PDF documents work like a charm on all kinds of devices.
MANUAL LIST:
RENR1389 – Disassembly & Assembly (3412C Generator Set Engine)
SENR1095 – Disassembly & Assembly (3408C & 3412C Marine Engines)
SENR1147 – Specifications (3408C and 3412C Marine Engines)
SENR5516 – Specifications (3408C, 3412C & 3412D High Performance Marine Engines)
SENR5517 – Systems Operation (3408C, 3412C & 3412D High Performance Marine Engines)
SENR5517 – Testing & Adjusting (3408C, 3412C & 3412D High Performance Marine Engines)
SENR7380 – Specifications (3408B & 3408C Industrial & Marine Engines)
KENR8699 – Schematic (3412C Generator Set with EMCP 3 Electrical System).pdf
SEBU6497 – Maintenance Intervals (3408C, 3412, 3412C & 3412D High Performance Marine Engines).pdf
SEBU6497 – Operation & Maintenance Manual (3408C, 3412, 3412C & 3412D High Performance Marine Engines).pdf
SENR1133 – Disassembly & Assembly (3408C & 3412C Marine Engines).pdf
SENR1148 – Systems Operation (3408C & 3412C Marine Engines).pdf
SENR1148 – Testing & Adjusting (3408C & 3412C Marine Engines).pdf
EXCERPT:
Individual fuel injection lines carry fuel from the fuel injection pumps to each cylinder. One section of line connects between the fuel injection pump and an adapter on the valve cover base. Another section of line on the inside of the valve cover base connects between the adapter and the fuel injection nozzle (3).
The fuel filters and priming pump are located in a compartment at the front of the fuel tank. The fuel transfer pump is mounted on a drive adapter on the fuel injection pump housing, and is driven by a shaft connected to the fuel injection pump camshaft. Fuel transfer pump relief valve (14) is located in the cover of the pump.
Fuel priming pump (13) is used before the engine is started to put pressure in the fuel system and to vent air from the system. A check valve (9) located in the fuel transfer pump adapter housing will let fuel go around the fuel transfer pump when the priming pump is in use.
There is no bleed orifice or valve installed on the fuel injection pump housing to vent air from this part of the fuel system. Air trapped in the fuel injection lines can be vented by loosening all of the fuel injection line nuts where they connect to the adapters in the valve cover base. Move the governor lever to the low idle position. Crank the engine with the starting motor until fuel without air comes from the fuel line connections. Tighten the fuel line nuts. This procedure is necessary because the fuel priming pump will not give enough pressure to push fuel through the reverse flow check valves in the fuel injection pumps of a direct injection system.
An automatic timing advance unit is mounted on the front of the fuel injection pump camshaft. It is driven by the engine camshaft gear inside the front timing gear housing. The automatic timing advance unit gives easier starting and smooth low speed operation. It will also advance timing as engine speed increases to give correct engine operation efficiency.
…
Usage:
34123JKBridge Adjustment (If Equipped)
When the head is disassembled, keep the bridges with the respective cylinders. Adjustment of the bridge will be necessary for the following reasons. The battle of polytopia crack.
- Grinding the engine's valves
- Resurfacing or reconditioning the engine's cylinder head
The bridge should be checked and/or adjusted when the valves have been adjusted. Use the procedure that follows to make an adjustment to the bridge.
Illustration 1 | g00363479 |
Bridge adjustment |
Note: Valves must be fully closed.
- Apply engine oil on the bridge dowel in the cylinder head. Apply engine oil in the bore in the bridge.
- Install the bridge with the adjustment screw toward the exhaust manifold.
- Loosen the locknut for the adjustment screw. Loosen the adjustment screw for several turns.
- Put a force on the bridge with a finger. This will keep the bridge in contact with the valve stem opposite the adjustment screw.
- Turn the adjustment screw clockwise until the adjustment screw makes contact with the valve stem. Then, turn the adjustment screw 20 to 30 degrees more in a clockwise direction. This will make the bridge straight on the dowel. Also, this will make compensation for the clearance in the threads of the adjustment screw.
- Hold the adjustment screw in this position. Tighten the locknut to 47 ± 9 N·m (35 ± 7 lb ft).
- Use clean engine oil to lubricate the contact points of the bridge assembly and the rocker arm.
Valve Lash Setting
Valve lash is measured between the rocker arm and the bridge for the inlet valves. Valve lash is measured between the rocker arm and the valve stem for the exhaust valve. All of the clearance measurements and the adjustments must be made with the engine stopped. The valves must be fully closed.
Valve Lash Check
An adjustment is not necessary if the measurement of the valve lash is in the acceptable range. The ranges are given in the following tables.
Quick Reference for Engine Valve Lash Setting 3408 Engines | ||
---|---|---|
Inlet Valves | Exhaust Valves | |
Valve Lash Setting | 0.28 to 0.48 mm (0.011 to 0.019 inch) | 0.66 to 0.86 mm (0.026 to 0.034 inch) |
TC Compression Stroke | 1-2-5-7 | 1-3-4-8 |
TC Exhaust Stroke (1) | 3-4-6-8 | 2-5-6-7 |
Firing Order | 1-8-4-3-6-5-7-2 (2) |

( 1 ) | 360° from TC compression stroke |
( 2 ) | Refer to the following illustration in order to locate the No. 1 cylinder. |
Quick Reference for Engine Valve Lash Setting 3412 Engines | ||
---|---|---|
Inlet Valves | Exhaust Valves | |
Valve Lash Setting | 0.28 to 0.48 mm (0.011 to 0.019 inch) | 0.66 to 0.86 mm (0.026 to 0.034 inch) |
TC Compression Stroke | 1-3-4-6-7-12 | 1-4-5-8-9-12 |
TC Exhaust Stroke (1) | 2-5-8-9-10-11 | 2-3-6-7-10-11 |
Firing Order | 1-4-9-8-5-2-11-10-3-6-7-12 (2) |
( 1 ) | 360° from TC compression stroke |
( 2 ) | Refer to the following illustration in order to locate the No. 1 cylinder. |
Note: The inlet and exhaust valve lash adjustments should be made at the first recommended oil change. Refer to Operation And Maintenance Manual for subsequent intervals.
Valve Lash Adjustment

Illustration 2 | g01015545 |
Cylinder and valve locations for 3408 engines (A) Inlet valves (B) Exhaust valves (C) Fuel injection pump |
Illustration 3 | g01015548 |
Cylinder and valve locations for 3412 engines (A) Inlet valves (B) Exhaust valves (C) Fuel injection pump |
Use a feeler gauge in order to measure the valve lash setting.
Illustration 4 | g00363480 |
Valve lash |
To make an adjustment to the valve lash, turn the adjustment screw in the rocker arm. Valve lash adjustments can be made by using the following procedure:
Illustration 5 | g00363481 |
Valve adjustment (typical example) |
Valve Lash | |
Valves | Thickness of Gauge |
Inlet | 0.38 mm (0.015 inch) |
Exhaust | 0.76 mm (0.030 inch) |
Adjust the valve lash while the engine is stopped. Use the following procedure in order to adjust the valves:
- Put the No. 1 piston at the top center position.
Note: See Testing and Adjusting, 'Finding Top Center Position for the No. 1 Piston' for further details.
- With No. 1 piston at the top center position of the compression stroke, an adjustment can be made to the valves.
Before any adjustments are made, lightly tap each rocker arm at the top of the adjustment screw. Use a soft mallet to ensure that the lifter roller seats against the camshaft's base circle.
- Make an adjustment to the valve lash on the inlet valves for the following cylinders.
For 3408 engines, adjust the valve lash on the inlet valves for cylinders 1, 2, 5, and 7.
For 3412 engines, adjust the valve lash on the inlet valves for cylinders 1, 3, 4, 6, 7, and 12.
- Loosen the valve adjustment locknut.
- Place the appropriate feeler gauge between the inlet rocker arm and the inlet valve bridge. Turn the inlet adjustment screw while the valve adjustment locknut is being held from turning. Adjust the valve lash until the correct specification is achieved. Refer to Table 3.
- After each adjustment, tighten the valve adjustment locknut while the valve adjustment screw is being held from turning. Use the following torque.
Engines with a bridge adjusting assembly Torque for the valve adjustment locknut .. 30 ± 4 N·m (22 ± 3 lb ft)
Engines without a bridge adjusting assembly Torque for the valve adjustment locknut .. 47 ± 9 N·m (35 ± 7 lb ft)
Recheck each adjustment.
- Make an adjustment to the valve lash on the exhaust valves for the following cylinders.
For 3408 engines, adjust the valve lash on the exhaust valves for cylinders 1, 3, 4, and 8.
For 3412 engines, adjust the valve lash on the exhaust valves for cylinders 1, 4, 5, 8, 9, and 12.
- Loosen the valve adjustment locknut.
- Place the appropriate feeler gauge between the exhaust rocker arm and the exhaust valve bridge. Turn the exhaust adjustment screw while the valve adjustment locknut is being held from turning. Adjust the valve lash until the correct specification is achieved. Refer to Table 3.
- After each adjustment, tighten the valve adjustment locknut while the valve adjustment screw is being held from turning. Use the following torque.
Engines with a bridge adjusting assembly Torque for the valve adjustment locknut .. 30 ± 4 N·m (22 ± 3 lb ft)
Engines without a bridge adjusting assembly Torque for the valve adjustment locknut .. 47 ± 9 N·m (35 ± 7 lb ft)
Recheck each adjustment.

Caterpillar 3408 Injection Pump Service Manuals
- Remove the timing bolt, and turn the flywheel by 360 degrees in the direction of engine rotation. This will position the No. 1 piston at the top center at the beginning of the exhaust stroke. Install the timing bolt in the flywheel.
- Make an adjustment to the valve lash on the inlet valves for the following cylinders.
For 3408 engines, adjust the valve lash on the inlet valves for cylinders 3, 4, 6, and 8.
For 3412 engines, adjust the valve lash on the inlet valves for cylinders 2, 5, 8, 9, 10, and 11.
- Loosen the valve adjustment locknut.
- Place the appropriate feeler gauge between the inlet rocker arm and the inlet valve bridge. Turn the inlet adjustment screw while the valve adjustment locknut is being held from turning. Adjust the valve lash until the correct specification is achieved. Refer to Table 3.
- After each adjustment, tighten the valve adjustment locknut while the valve adjustment screw is being held from turning. Use the following torque.
Engines with a bridge adjusting assembly Torque for the valve adjustment locknut .. 30 ± 4 N·m (22 ± 3 lb ft)
Engines without a bridge adjusting assembly Torque for the valve adjustment locknut .. 47 ± 9 N·m (35 ± 7 lb ft)
Recheck each adjustment.
- Make an adjustment to the valve lash on the exhaust valves for the following cylinders.
For 3408 engines, adjust the valve lash on the exhaust valves for cylinders 2, 5, 6, and 7.
For 3412 engines, adjust the valve lash on the exhaust valves for cylinders 2, 3, 6, 7, 10, and 11.
- Loosen the valve adjustment locknut.
- Place the appropriate feeler gauge between the exhaust rocker arm and the exhaust valve bridge. Turn the exhaust adjustment screw while the valve adjustment locknut is being held from turning. Adjust the valve lash until the correct specification is achieved. Refer to Table 3.
- After each adjustment, tighten the valve adjustment locknut while the valve adjustment screw is being held from turning. Use the following torque.
Engines with a bridge adjusting assembly Torque for the valve adjustment locknut .. 30 ± 4 N·m (22 ± 3 lb ft)
Engines without a bridge adjusting assembly Torque for the valve adjustment locknut .. 47 ± 9 N·m (35 ± 7 lb ft)
Recheck each adjustment.
Caterpillar 3408 Marine Engine Specifications
- Remove the timing bolt from the flywheel after all valve lash adjustments have been made.
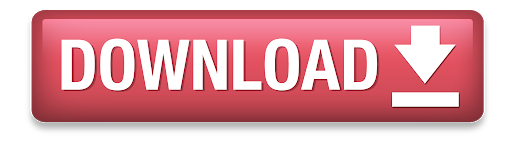